We will talk about adjusting air compressor pressure switch because we found it very hard to find a good tutorial. There is a lot of stuff out there that tells you how to do it and what tools you'll need, but not many articles show you the process step-by-step. So this is our attempt at giving people some help explaining why they would want to adjust their air compressor's pressure switch and how to do so without getting themselves into trouble.
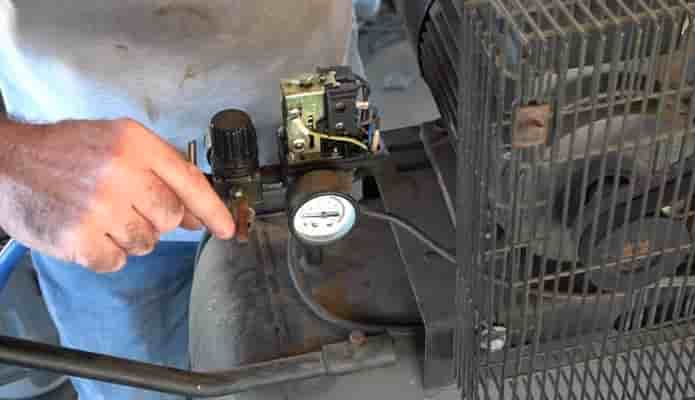
Air compressor pressure switches are devices that regulate the amount of air a pneumatic tool can use. In addition to regulating output from compressed air sources like kits and portable compressors, they also protect the equipment it attaches to by recycling the air when leakages occur or releasing air in stages depending on what tool is attached.
Air compressor pressure switches operate in response to changes in the air pressure of an air compressor. They usually send a signal to start the motor when the air pressure drops below 70 PSI and stop it when it reaches 87 PSI.
An air compressor pump turns on when the air pressure drops below the predetermined threshold. This device is more common in larger air compressors. It also helps protect your equipment from starting and stopping under extreme changes in demand or power outages since the excess demand won't shut down the unit when it reaches overpressure. Switching between mechanical relief valves and pressure switches will permit a malfunctioning valve to continue operating while still protecting your equipment by shutting off other lines of operation as needed to avoid excessive pressures. Some companies prefer using both devices for added protection, but some only use one type or the other entirely, depending on their preferences.
When Should I Check and Adjust My Air Compressor’s Pressure Switch?
It's best to check the air compressor pressure weekly.
But, first, let's talk about how air compressors work. Your typical air compressor has a pressure switch that will turn off the motor when it senses that the desired amount of water has filled up. So, suppose the desired quantity of water is 13 degrees, and you want your temperature gauge reading to remain at a steady 130 degrees Fahrenheit. In that case, your compressor should be running with enough pressure so that you will only need to adjust it once every three months or so in order for this to happen. On the other hand, if you notice your motor keeps shutting off before reaching 13 psi, it may mean an issue with leaks or its parts are clogged and need more of an overhaul than just a quick adjustment.
Why Should You Adjust the Air Compressor Pressure Switch?
A compressor, or pump, operates as the heart of a pneumatic system, and the air pressure must be maintained to allow for a proper working environment. An automatic adjustment mechanism regulates this air pressure called the adjustable regulator or air compressor pressure switch, and if not adjusted at regular intervals, it can lead to equipment failure.
The air compressor pressure switch prevents premature wear on the engine, reduces noise, and extends your equipment's motor life and useful service life. For these reasons, it is important that you periodically adjust this item according to the frequency mentioned in your owner's manual. Doing so will ensure optimum efficiency as well as safety for your personnel.
The best thing to do is have someone knowledgeable adjust this machine regularly or contact a professional so they can come out and address your needs promptly. It's always better to be safe with important pieces of equipment rather than sorry if a problem arises.
Related: What Size Air Compressor Do I Need for Impact Wrench?
What Can Happen If You Don’t Adjust Your Air Compressor Pressure Switch?
If your air compressor pressure switch is set too high and you're using an oil-free model, the load on the drive motor increases, which in turn increases bearing noise. As a result, it will reduce the lifespan of your compressor. Furthermore, suppose your air compressor pressure switch is too low but needs to be higher with what's going on for pressure to work properly. In that case, there are possible burn up risks for the motors and chemical corrosion problems for metal parts that extend over time. It's important to adjust and monitor these regularly to have an optimal running efficiency of all systems. These modifications must happen quickly because neglected scenarios lead toward extreme catastrophes in less than a minute! One last issue that can occur would be insufficient airflow to run the system at the right pressure.
Just as a note, you will need factory service manuals for your air compressor to adjust these aspects properly, and it's not recommended to do this without training, so don't just jump into doing something that could lead toward problems.
Adjust Air Compressor Pressure Switch (Step By Step Guide)
An Air compressor pressure switch is a safety device installed in an air compressor system to protect the system from running under low pressure.
When there's no demand for compressed air, it will shut down the motor and stop the compressed air supply from protecting equipment and workers from potential injuries due to insufficient operating pressure.
On this page, we are going to discuss how to adjust air compressor pressure switch?
Step 1: Check if there is the power to the unit or not. If no power comes in when you turn on the breaker, try resetting circuit breakers and fuses as required.
If there is electricity in your air compressor, but you still can't get any compressed air out of it, make sure that your electric filter switch is faulty or is tripped.
Step 2: Check the air pressure regulator, adjust air pressure to 3-4 bar. After you've adjusted the air regulator, please turn on the electric switch again and make sure that it works properly.
When your system runs in normal condition with sufficient pressure, you can proceed to the next step. But suppose your compressor motor keeps running or doesn't normally respond due to defective parts such as cylinder head, high and low-pressure valves etc. In that case, you must replace them first before adjusting the air compressor pressure switch.
Step 3: Remove the electrical plug from the metal box on top of the compressor, now take off screws from the cover. Open up cover carefully and inspect for any damages such as cuts or cracks near the wiring harness of this pressure switch.
If you found any damage, consult a professional to get advice on adjusting the air compressor pressure switch with safety, then replace damaged parts.
Step 4: Inspect this pressure switch's wiring harness and attached electrical terminals carefully for any problems such as damages or loose connections, etc. They may cause the system not to run normally due to low operating pressure even though it is adjusted properly.
Step 5: If your air compressor normally works after resetting electric filters and replacing its components so far, you can now adjust the air compressor pressure switch.
First, make sure that there's no electricity in your unit before touching anything inside the metal box on top of the compressor (the power must be off during this process).
Step 6: Remove the pressure switch plug with the spanner wrench, then loosen nuts of adjustment screws on both sides.
Then rotate the adjustment screw clockwise to increase air compressor pressure or counterclockwise to decrease until you reach your required operating pressure, in which case it should stop turning automatically; if not yet reached, you must go back one step to reset electric filters and check components again.
Now tighten both adjusting screws (left and right) firmly by applying pressure onto the metal box.
Step 7: install the plug into the electrical socket correctly; turn on the power supply and make sure that it normally works without tripping the circuit breaker (if your unit runs without tripping breaker but still no compressed air comes out, there might be something wrong with the motor or other parts, which require further inspection and repair).
If your system still doesn't work normally and trips circuit breaker every time you turn on the power supply, try resetting circuit breakers and fuses as required until it works properly.
Step 8: if all these steps are completed successfully without any problem, then test the unit by gradually increasing pressure to around 7 bar for 5 minutes to see if there is any abnormal sound or vibration; if no problem is found, switch off the power and check the air filter carefully. If it's dirty or clogged up with dust, clean or replace it immediately (clean filters regularly can prolong their service life forever); also check regeneration of moisture separator periodically during humid weather.
If everything in your compressor is working properly now except it's noisy or vibrates too much at the initial stage, it might be due to short-term problems such as air leakage, loose fittings etc., which also can cause your circuit breaker tripping. It's better to get professional advice on adjusting air compressor pressure switches for leaky fittings; otherwise, you need to replace them before adjusting more carefully.
Step 9: if all of the above steps are done and tested successfully but still not enough compressed air comes out from the pipe, loosen the high-pressure valve adjusting screw slightly by using a spanner wrench (it should turn very little) tighten it fully until no compression occurs. Loosen low-pressure valve adjusting screw counterclockwise by turning gently with spanner wrench (it should turn very little) then tighten it fully until no compression occurs. Now test the unit and see if there's any problem with pressure after adjusting high and low-pressure valves properly.
If your air compressor still doesn't normally work after all the above steps, try to consult a professional engineer for advice; make sure that they have good knowledge about air compressors as they may provide you with wrong instructions on how to adjust the air compressor pressure switch which can cause more damage to your system.
Step 10: If you have a regulator built-in into your compressed air system, adjust its valve slowly by turning clockwise gently with a spanner wrench until there is no fluctuation in operating pressure etc., then tighten firmly but do not over-tighten.
That's It! Once you are done with these four steps, double-check that everything is working correctly before returning anything to normal operating conditions and procedures.
Watch the video on how to adjust the air compressor pressure switch control valve:
5 Benefits of Adjusting Your Air Compressor’s Pressure Switch
The benefits of adjusting your air compressor's pressure switch are huge and cover most of your maintenance needs. Here are the top 5 benefits you will get by adjusting or replacing it.
#1: Your air compressor will last longer
Air compressors include a pressure switch to regulate the amount of air being produced. Even though they're very reliable, their reliability might decrease, and that's why they should be regularly inspected for any potential problems or adjusted if needed. Read more here about how to inspect them properly. When there is an issue with this component, your compressor won't produce enough PSI (pounds per square inch) and even worse – even when there isn't one, but only the faulty indicator light on. To adjust or replace the pressure switch every once in a while so you can keep your compressor in a good and healthy operating condition.
#2: You'll extend the life of your air tools
Some air compressors have an adjustment feature for low/medium/high PSI, while others are constant pressure output. If you have the second type, you know that it produces different amounts of PSI depending on which tool you're using. The problem is that some tools might overheat or even burn up if they aren't used at the right pressure setting. For example, screwdrivers require 100-120 PSI, while high-pressure tools such as impact wrenches need 240+ PSI. If you set them to run at 80-90 PSI which is the optimum requirement when working in a garage with other air tools, unfortunately, they won't do you much good. On the other hand, some of the best and most useful tools are my impact wrench and a large compressor. So set your pressure switch to the right settings, so all your air tools work as efficiently as possible.
#3: You'll save tons of money
If your air compressor is constantly running at low PSI output instead of its optimum range, then it's going to run for a long time without any issues (as long as you maintain it properly by cleaning the debris from time to time). And because a constant high-PSI output cannot produce more than what the hose or gun requires, you're wasting energy, hence extending your electricity consumption, which will cost you a lot of money in the long run. So adjust your pressure switch to permanent high-PSI output, and you'll save on electricity bills.
#4: You'll have fewer problems with disposal
The air compressor will produce condensation as it performs the compression process. This can be a problem if there are no provisions for proper drainage. One common result is that water accumulates near or below the base, and moisture gets into the electrical components, damaging them. If there is a provision for draining, but it's damaged, you might as well end up with irreparable damage, which means replacement cost and time spent waiting for its delivery. As far as I know, some compressors come with an adjustable drain valve so you can set it to a proper setting that is low enough to prevent any leaks yet high enough for the water to drain.
#5: You'll make maintenance easier
If you have an adjustable pressure switch, it's going to be easier and faster when adjusting the PSI because you only need to turn one knob instead of many (this also helps in case you don't want to use your compressor for some time). In addition, some units come with a digital LCD so you can see the current PSI output at all times. And if you're lucky, your unit has a built-in LED light which will indicate that the compressor is making noise (indicates there is no blockage) and running correctly.
You might be wondering!
Don't waste time on the wrong compressors. Check out this list of our top picks for air compresses that will work best with Impact Wrench!
Final Words
You now know how to adjust air compressor pressure switch, and you are ready for any future problems that might arise. A well-adjusted air compressor will be sure to last a long time without requiring repair or replacement. Remember these steps when adjusting your machinery to save money and maintain efficiency. In addition, we hope this blog post has been helpful as an educational resource on how to adjust air compressor pressure regulators! Thank you for reading - if there is anything else we can do, please feel free to reach out at any time!